Protection of Diesel Generators
and Machinery Spaces
Stationary diesel engines are often coupled with generators for primary or emergency power generation. They are also used to drive pumps and compressors in the petrochemical and gas-pipeline industries and with co-generation gas turbine installations.
The investment directly associated with these engines is fairly high but that is often only a fraction of the value for the service they provide. Losing them to fire damage often has dramatic consequences for the user and ultimately leads to business downtime which can never be afforded. The cost of this downtime can be catastrophic to a company or to a small community when for example, the generator provides power to an entire village, as is often the case in remote areas.
Diesel engines come in various sizes and configurations and the main hazard is associated with combustible or flammable liquids. The fire hazard is mainly centred around the fuel and lubrication systems and include:
- Ignition of the fuel in case of leaks on hot surfaces;
- Lubricants, hydraulic fluids and sometimes, even the fluid being pumped or compressed;
- Ignition of flammable vapours or combustibles in storage close to the diesel engine;
- Pool fire from the fuel or lubricant leaking from a break in the equipment.
Diesel engines will produce temperatures easily reaching 538 ℃ near manifolds, exhausts and mufflers that can easily ignite any combustible coming in contact with them, such as building penetrations, and require special precautions.
Design
with ICAF
In this example, protection is required for a diesel engine room containing three generators side by side. In this case, the room is simply flooded with Compressed Air Foam (CAF) from nozzles installed in the ceiling as shown on Figure 1 below.
NFPA-11, TIA #05-1 in art. 7.15 states that where fixed spray type systems are used to protect room enclosures, the minimum density shall be no less than 1,63 L/min/m². Furthermore, system discharge duration shall be designed for a minimum period of 10 minutes for deluge-type systems (art. 7.16).
The quantity of foam concentrate is reduced by using the ICAF Systems since its high efficiency is achieved while using only a 2% concentration of AFFF foam concentrate instead of the usual 3% !
Using FireFlex Systems FM Approved ICAF Design Manual, the designer will locate a grid of total flooding nozzles to cover the generator room area.
The designer has to take site conditions into consideration before deciding which design will best protect the hazard. In some cases, additional nozzles may need to be installed directly at the generators and careful evaluation of the various hazards should be made to determine if they are required.
Problems
with the use traditional technologies
Typically, diesel engine installations are protected using traditional fire sprinklers. In the case of remote locations, water supply quickly becomes an issue preventing their use.
They are also frequently protected by fixed Carbon Dioxide systems (CO2) but with the recent casualty rates from accidental discharges on the increase and new environmental concerns about gases that contribute to the green house effect, they are rapidly losing popularity with users.
Similarly, diesel engines are sometimes protected by dry chemical systems but the risk of corrosion to the equipment by the extinguishing agent is often a problem, especially in the case of an unattended installation.
Other installations are sometimes protected with clean agent systems but some of them will decompose on contact with the engine hot surfaces, producing highly corrosive or toxic chemicals, damaging for the equipment and / or people on the premises.
Typical to gaseous systems in general, the enclosure integrity should also be maintained at all times and this is often a problem in actual working conditions, severely limiting the ability of extinguishing gases to extinguish the fire.
Project
Scope of Work
This simple installation will provide foam coverage on the surfaces of the generators themselves but also on the floor around them, thus providing protection in case of fuel leaks. Figure 1 (see below) shows a typical ICAF System installation with its grid of discharge nozzles installed at ceiling level. The balanced flow piping is simple to install and of smaller diameter than the equivalent foam-water system, reducing the costs for the installing contractor.
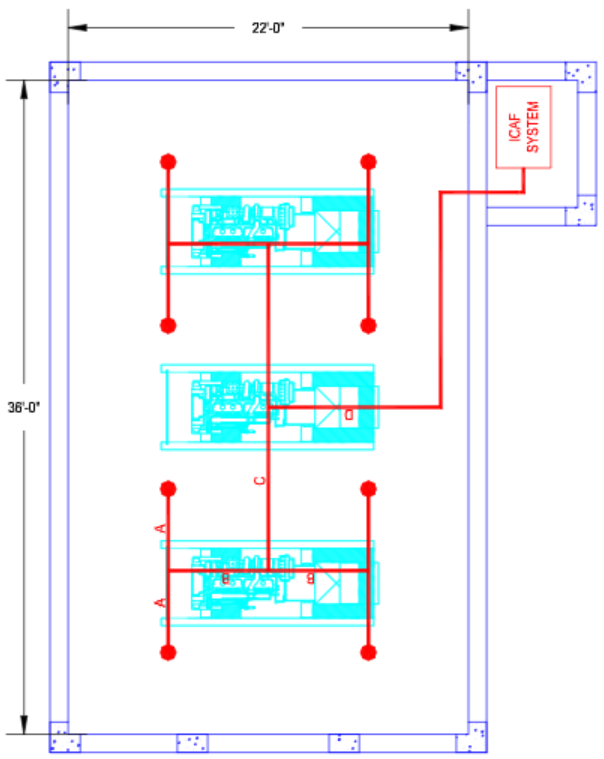
Figure 1
CAF nozzle layout
The ICAF system required for protecting this hazard includes a 37,8L tank of foam concentrate with two (2) compressed air cylinders, representing a small foot print (Figure 2 see below).
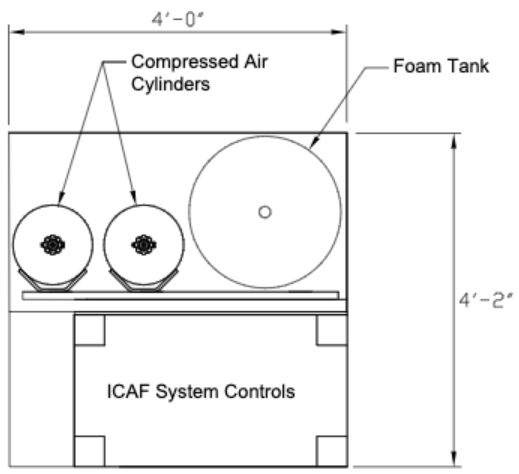
Figure 2
ICAF System footprint
The ICAF system requires so little water that even if the local water supply was inexistent, as is often the case in remote locations, the problem could be easily resolved by installing a water reservoir of 1892,7L capacity that is pressurized on system activation. The system would then be completely stand-alone and this critical installation would be adequately protected.
Conclusions
Fire protection designers now have an additional weapon in their arsenal of fire combat tools. The ICAF technology is emerging as an environmentally friendly solution for protection of diesel generators, machinery rooms and other similar hazards.
With ICAF Systems installed on their premises, plant owners can now better protect their investment while achieving total fire suppression in case of accidental fires.
Should you have questions regarding this application or any other involving generators, contact SIRON Compressed Air Foam. Our engineers will work the project out with you and find the best layout for your specific application.